Customized Dosing Systems
In the field of dosing and pump technology, the requirements and dosing processes of our customers are very different. Individual challenges must be recognized and solved.
As a system provider for dosing technology, sera is able to understand these different processes and to develop tailor-made solutions for every customer requirement.
Municipal Utilities Winterberg
Winterberg, a centre of tourism in the Sauerland region with 13,000 residents across 15 districts, has experienced a development boom in recent years and – from the point of view of tourism – has all the features of a typical destination in the central German uplands.
In order to give winter sports enthusiasts 80 days of guaranteed snow a year, a plan was drawn up in the 1990s to make snow. The scheme worked: in 2012, Winterberg recorded more than 1 million overnight stays for the first time - and that was in commercial hotels alone. Unrecorded stays with small and private accommodation providers and about 1.5 million day visitors a year should be added to this.
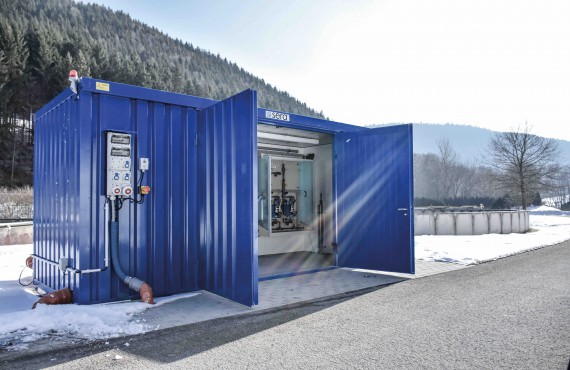
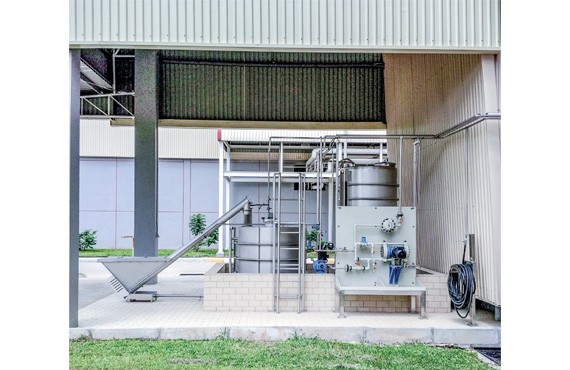
Phnom Penh - Heineken Brewery
Approximately 50 million tons of caustic soda are produced annually and used in various ways in industry. sera offers a cost-effective system solution specifically for use in the food industry, which has a variable but large demand for alkaline cleaning agents such as caustic soda. This enables the secure and efficient preparation of caustic soda based on sodium hydroxide (NaOH) in solid form (pellets, flakes, pearls or powder) and water.
Bonn - Waste incineration
Recycling of the waste from Bonn and the surrounding region is carried out by Müllverwertungsanlage Bonn GmbH (MVA), a subsidiary of Stadtwerke Bonn (Bonn Public Utilities). Over 1,000 tonnes of waste, which has to be disposed of in a safe and environmentally friendly way, is delivered to it every working day. In a complex thermal process, the waste is first incinerated and then processed. Flue gases are created when the refuse is burnt.
Full article: THE WASTE RECYCLING PLANT IN BONN - ENERGY GENERATION WITH THE LATEST TECHNOLOGY - sera NEWS (sera-web.com)
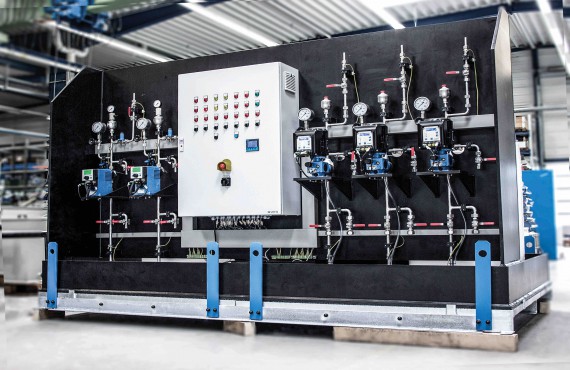
Examples of customer-specific systems
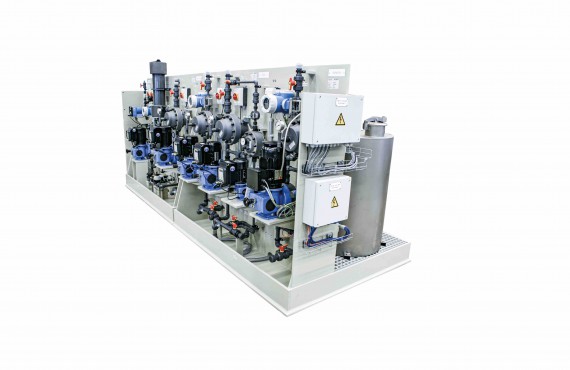
DEFOAMER DOSING
- Storage tank
- Dosing
- Messuring technology
- Electrical engineering
In terms of design, the individual parameters and our customer requirements are implemented by the sera Group’s internationally networked engineering department, ensuring the customer receives a customised solution for their task – everything from a single source!
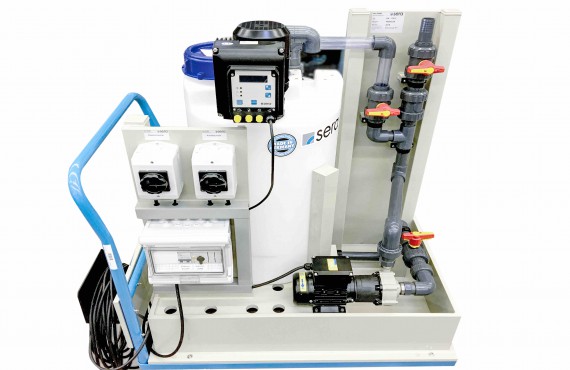
PORTABLE MIXING AND DOSING STATION FOR THE CHEMICALS INDUSTRY
-
Mobile platform truck with 100-litre dosing tank featuring agitator, fluid level gauge and other fittings
-
Centrifugal pump for transferring chemicals during the customer process
-
Collecting basin in case of leakage
-
Control panel for on-site operation
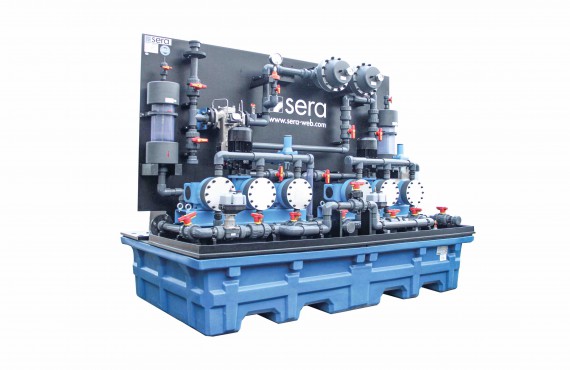
PRESSURE BOOSTING SYSTEM FOR ADBLUE IN THE AUTOMOTIVE INDUSTRY
-
Dosing system for the automotive industry (urea
-
Two pumps of type MK/MF/MK410.2-1450e, each with three pump heads
-
Max. delivery rate 4,350 l/h per pump and low pulsation
-
Safe operation and easy service thanks to two electric diaphragm valves and the installed ball valves
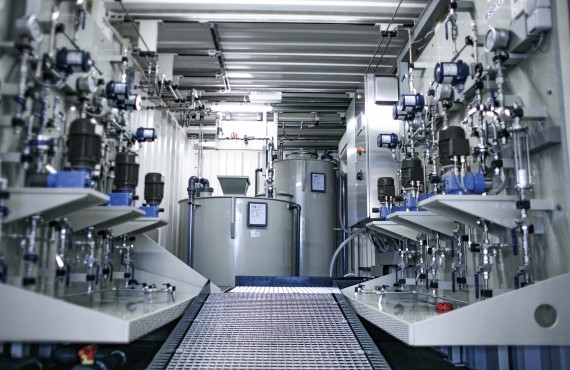
DOSING CONTAINER FOR SODIUM PHOSPHATE
-
Dosing container for saline ambient air with special coating
-
Climate-control system to keep interior temperatures constant
-
Dosing unit for sodium phosphate with multi-layer diaphragm pumps
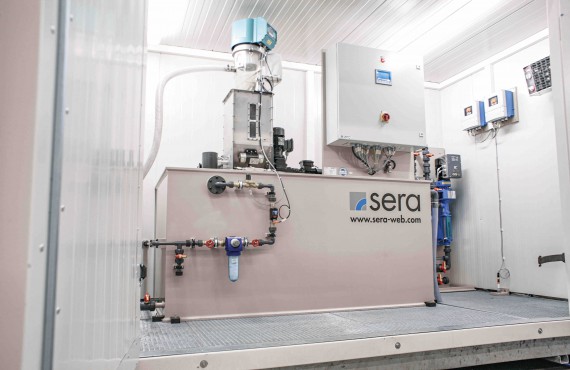
PREPARATION AND DOSING UNITS FOR POLYMER SOLUTIONS IN THE CLOSED CONTAINER
-
Weather-protected and heat-insulated container including heating system, lighting and ventilation
-
Container features built-in 3-chamber polymer continuous flow systems (type: PolyLine Flow 2000 S)
-
Dry material feeder with small-parts conveyor device and 200-litre storage tank for polymer dry materials
-
Two eccentric screw pumps with frequency converters to remove polymer solution when ready for production
-
Entire unit features central control cabinet (SPS technology) including customised programming
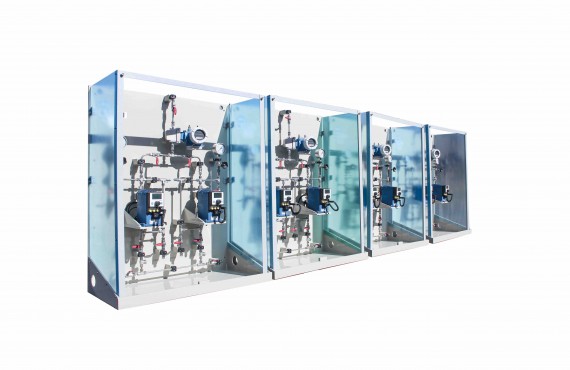
DOSING OF SULPHURIC ACID
-
Dosing systems with innovative stepper motor pumps and flow measurement for maximum precision
-
System piping made of stainless steel with stand-by construction and design
-
Maximum safety thanks to spray guard, intelligent diaphragm monitoring and operating condition notifications

DOSING OF SODIUM PHOSPHATE AT POWER PLANTS
-
All-in-one dosing station on a gridiron with collecting basin
-
Two high-pressure pumps with multilayer diaphragm technology ensure optimum dosing precision
-
Stainless steel preparing tank and control cabinet for automatic operation of the systems
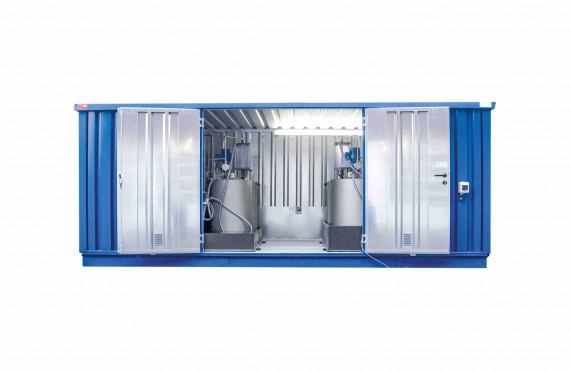
CONTAINER FOR DOSING AMMONIA SOLUTIONS AT POWER PLANTS
-
Two completely assembled dosing systems with collecting basins in one container with double doors
-
Location can be determined by the client; easy to retrofit
-
Two complete dosing stations each with two dosing pumps and one preparation pump to ensure optimum availability of chemicals

ROBUST UNITS FOR EXTREME ENVIRONMENTAL CONDITIONS
-
Single-layer diaphragm pumps with stainless steel heads and a capacity of 1,450 l/h in a stand-by design
-
Stainless steel frame construction for floor installation with drip tray and piping made of stainless stee
-
Pressure manometer and stainless steel pulsation damper for ideal operation
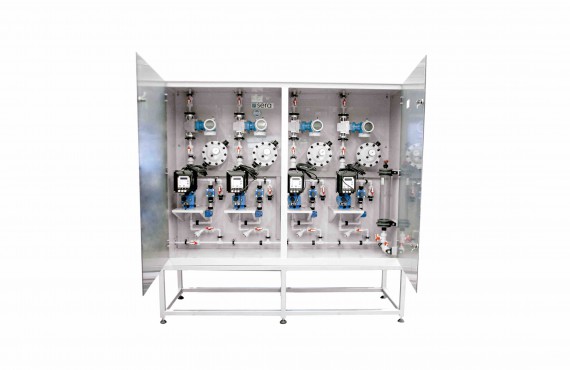
DOSING SYSTEM IN THE PROTECTIVE CABINET
Sample application
Dosing of external carbon sources such as methanol, ethanol, acetic acid and glycol
Design
The completely modular design of our dosing systems facilitates simple adaptation to individual dosing requirements. The system is designed in accordance with the ATEX directive, as required for handling flammable liquids such as methanol.
Features
- Compact, space-saving design
- Pump type and size to meet requirements
- Piping systems made of PVC-U, PP, PVDF or stainless steel
- Assembly panel with collecting basin and drain
- Assembly panel - with base frame as an option
- Leakage sensor with building regulation approval
STAINLESS STEEL DOSING SYSTEMS
When mixing caustic soda from solids, an exothermic reaction with temperatures of up to 95 °C occurs. The sera CausticPrep is designed so that the user can easily feed the caustic soda flakes into the process from a safe distance.
Sample application
Preparation of caustic soda from pellets and flakes.
Design
The stainless steel hopper is filled with solids by means of a screw conveyor; these solids are fed into a feed hopper by the operator. The safety of the user is ensured by the distance to the hot tank.
Available Sizes
- 1 m3 batching tank / 2 m3 batching tank / 3 m3 batching tank / 5 m3 batching tank
Features
- Medium-affected parts are made of stainless steel
- Debagging with screw conveyor approx. 1000 kg/h
- Level indicator with shut-off valve
- Electric agitator
- Temperature display
- Overflow pipe with siphon
- Manual addition of water
- Tubular safety guard
- Debagging station is kept away from the hot areas
Accessoires
- Suction device
- Transfer and refill station
- Storage tank
- Dosing station